PROBLEM TARGETED
Every year in Europe there are 65 million people skiing and every skier needs high quality ski boots with good performances, safety characteristics and ergonomic comfort.
Ski boots are composed of a hard-outer shell for support and a soft liner for comfort and warmth; over the years the European Industry has managed to maintain the worldwide leadership to impeccably build ski boots and nowadays 98% of the 3,5 million pairs of ski boot produced yearly are made in Europe.
(Source: International Ski Federation)
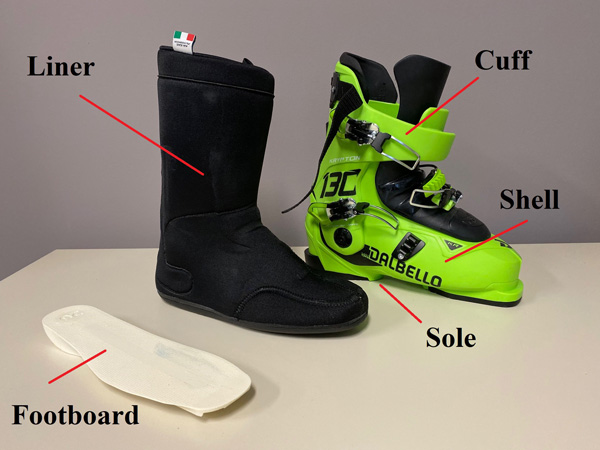
Each ski boot is composed of more than a hundred plastic parts, mainly assembled by means of connectors. The external part is made with thermoplastic materials and the internal part (Liner) is made of foamed materials with different densities and in several parts made of sandwiches of materials kept together by glues.
Time and use rapidly degrade ski boot materials:
- after 50/80 skiing days the liners comfort level starts decreasing with a deterioration due to foot pressure and temperature/humidity conditions.
- after 150/200 skiing days the outer shell transmission of loads from the skier to the ski edge starts to get worse and the control of the ski is no more safe and precise: so there comes a point when the ski boots must be substituted (Average lifespan is 3 years for rentals and 5 years for private individuals) which at present means bringing all ski boots to disposal.
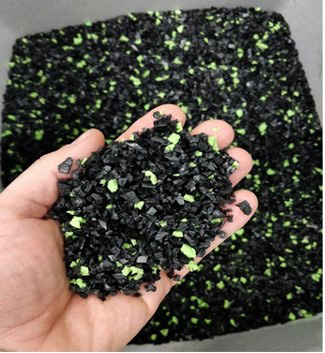
The recovery of post-consumption ski boots has been attempted by some producers in the past, but it failed mainly for disassembling and material separation costs of the large number of components and for the absence of a method for sorting and recycling the liner which is composed of foamed material sandwiches. Since all post-consumer ski boots are sent to landfill, there is a relevant environmental problem due to large amounts of soft and hard plastics that are not recycled.
An additional environmental problem is related to the generation of pre-consumer scraps during the cutting process for liner manufacturing, that at present time are completely landfilled or disposed through incineration with energy recovery; the liner foamed material scraps can be up to 40% of the total material used.
Nowadays the 3,5 million pairs of ski boots produced yearly worldwide are entirely made of virgin materials and landfilled after 3/5-year use.
This means: